Our History
Our Legacy of Excellence: The ClearFox® Journey
- 2007 - Foundation
- 2008 - Development
- 2009 - Market Revolution
- 2010 - Patents
- 2011 - Research
- 2012 - Leadership
- 2013 - Advancements
- 2014 - Expansion
- 2015 - Market Diversification
- 2016 - Certification
- 2017 - Standardization
- 2018 - Innovation
- 2019 - Relocation
- 2020 - Customer Experience Center
- 2023 - New Milestones
- 2025 - International Standards
Foundation and Vision (2007-2008)
ClearFox® began as PPU Umwelttechnik GmbH, founded by Dipl.-Ing(FH) Wolfgang Pöhnl alongside leading wastewater specialists in Kemnath, Germany. From our inception, we envisioned revolutionizing wastewater treatment through innovative, modular solutions.
- 2007
Strategic Expansion and Brand Development (2008)
Recognizing the importance of global connectivity, we relocated to Bayreuth to capitalize on superior transportation infrastructure. This strategic move enabled us to specialize in modular container sewage treatment plants distributed worldwide under our proprietary ClearFox® brand. Our commitment has always been to deliver adaptable solutions using diverse process technologies tailored to specific market requirements.
Market Revolution (2009)
A pivotal moment arrived with the introduction of ClearFox® nature – a groundbreaking electricity-free domestic sewage treatment system. After receiving comprehensive European approvals, this innovative solution began displacing conventional sewage plants globally, establishing our reputation as industry disruptors alongside our established ClearFox® SBR plants and Retrofit Kits.
Innovation and Patents (2010)
We enhanced our ClearFox® flotation system through advanced production optimization, incorporating improved sludge discharge via airlift technology. This breakthrough resulted in a patented OEM product now utilized by plant manufacturers worldwide.
- 2010
Research Excellence and Strategic Partnerships (2011)
Our commitment to innovation led to the expansion of our wastewater laboratory for comprehensive pilot testing, enabling bespoke industrial wastewater solutions. Under the guidance of internationally acclaimed wastewater specialists, we simultaneously developed strategic partnerships with contract manufacturers, providing specialized aquaplast tools to ensure superior quality and enhanced productivity.
Container Technology Leadership (2012)
We pioneered standardized production of FBR reactors and lamella separators within sea containers, utilizing proprietary aquaplast hollow body technology for watertight container lining. This innovative construction method, distinguished by exceptional chemical resistance and elimination of underwater welding seams, became an industry standard at PPU.
Specialized Applications Advancements and Milestone Deliveries (2013)
Our engineering team developed an advanced variant of the proven cascaded ClearFox® fixed-bed, specifically for high nitrogen load wastewater treatment, including liquid manure and fermentation residue processing. Simultaneously, we achieved a significant milestone, delivering our first ClearFox® nature systems in prefabricated concrete tanks and over 5,000 units in aquaplast PE tanks by year-end.
Quality Assurance and Sector Expansion (2014)
We expanded our Bayreuth facility to include dedicated sample construction and testing areas, ensuring rigorous quality control for our contract manufacturing partners. Our enhanced capabilities enabled comprehensive food and beverage sector solutions, covering the complete spectrum from pre-treatment to wastewater reuse through prefabricated modules.
Market Diversification and Regional Services (2015)
Strategic expansion included additional Bavarian storage facilities and the launch of our leasing division. Our rapid-deployment capability for the German-speaking D-A-CH region (Germany, Austria, Switzerland) established us as the preferred partner for temporary wastewater treatment solutions.
Certification Excellence and Global Expansion (2016)
After rigorous one-year testing, our ClearFox® FBR bioreactor achieved certification for COD degradation up to 100 kg per container daily – the world’s only certified high-performance containerized bioreactor. With over 80 units now produced annually, we strengthened our global presence through strategic partnerships and international sales expansion.
Technology Standardization and Scale (2017)
We standardized our proven QuickQNE+ technology for large-scale applications exceeding 5,000 population equivalents. This single-chamber SBR plant with sludge stabilization now serves our global partner network, with contract manufacturers producing over 1,500 plug-and-play biotreatment plants annually.
Scalability and Research Innovation (2018)
The introduction of rectangular ClearFox® DAF systems in HC sea containers enabled scalable solutions from 50m³/h to over 300m³/h through parallel connectivity, facilitating daily treatment volumes exceeding 5,000m³. Concurrently, we initiated groundbreaking research into biocomponent fiber development for enhanced nitrogen decomposition bacteria (Project Biocomps, completed 2022).
Infrastructure Excellence (2019)
Our relocation to the state-of-the-art 4,500m² facility on Carl Kolb Strasse, Bayreuth, consolidated our sample construction, engineering, laboratory, testing, production, and technical processing operations under one roof, optimizing operational efficiency.
Customer Experience and Training Center (2020-2021)
Despite global challenges, we completed expansion of our Bayreuth headquarters, adding a visitor lounge and dedicated wastewater system sampling and testing facility. This enhancement creates an optimal environment for international customer consultations and comprehensive training programs for supervisors, operators, and partner companies in system operation and maintenance.
New Project Milestones (2023-2025)
We continue to push the boundaries for both our products and projects. In 2023-2025 we completed our largest municipal wastewater treatment project to date, using containerized FBBR modules for a population of 20,000 persons. We also continued to supply our modular FBBR systems for specialised camp applications – with systems being supplied to the British Antarctic Survey in Antarctica, and also solutions being supplied to US military projects.
International Standards Achievement (2025)
ClearFox® achieved comprehensive ISO certification across multiple critical standards, reinforcing our position as a world-class wastewater treatment solutions provider. Our certifications include:
ISO 9001:2015 – Quality Management Systems: Demonstrating our unwavering commitment to consistent service delivery, customer satisfaction, and continuous improvement across all operations. This internationally recognized standard ensures our products and services consistently meet the highest quality requirements while maintaining regulatory compliance.
ISO 14001:2015 – Environmental Management Systems: Validating our systematic approach to environmental stewardship, resource optimization, and pollution prevention. This certification underscores our dedication to minimizing environmental impact while enhancing operational sustainability throughout our manufacturing and service delivery processes
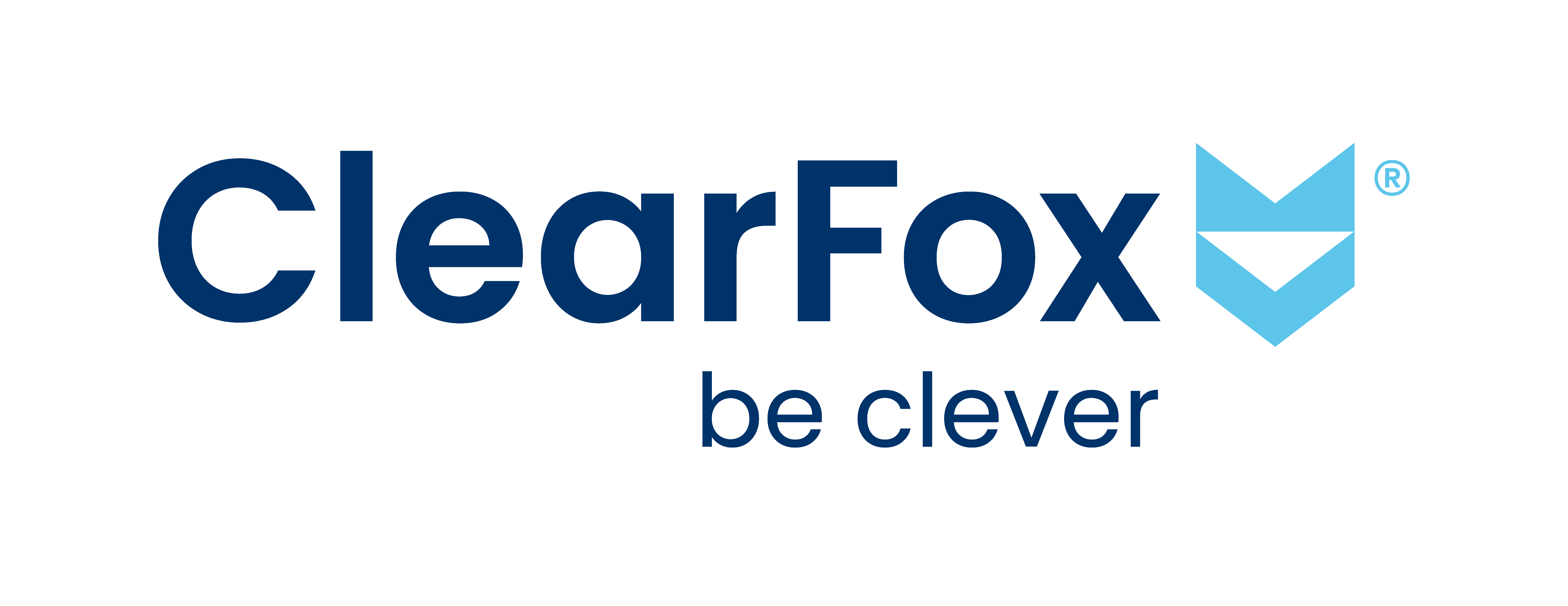
- 40,000+ treatment systems
- Installed in over 50 countries
- Treating 25 million litres daily
- Certified.
- Compact.
- Containerized.
- [Clever]
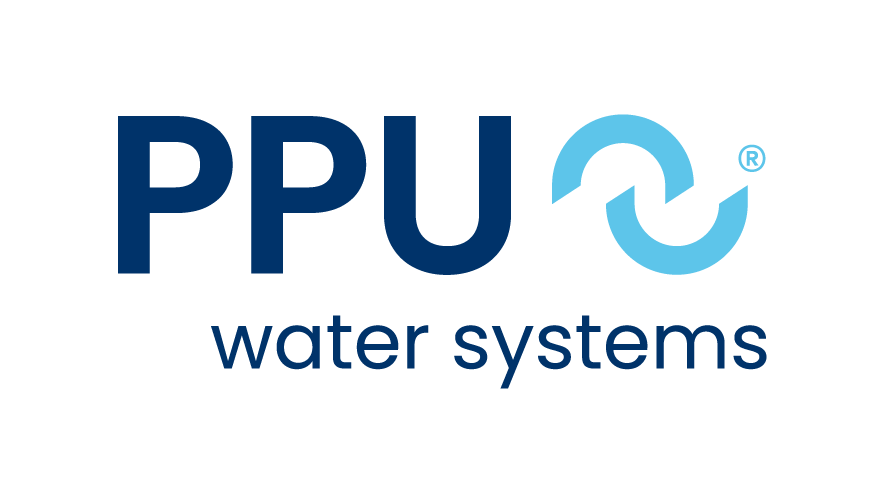